Six Sigma is a methodology that aims to drive process improvements by drastically reducing defects and costs. This guide explores the fundamental principles and effective tools, including the well-known DMAIC and DMADV frameworks. To achieve near-defect production, with less than 3.4 defects per million units, Six Sigma has become an indispensable tool for many.
What is Six Sigma?
Six Sigma (6σ) is a methodology that helps you improve processes through improvement projects. Six Sigma focuses on reducing errors and cutting costs by measuring defects and variations that exist in an ongoing process and systematically eliminating them.
The relationship between input and output is important in Six Sigma. To create a better product or service, you need to improve what you put in, to get something better out. The methodology is often associated with the manufacturing industry, but companies such as Microsoft, Amazon, Maersk, Google, and Bank of America are well-known examples of companies that use Six Sigma.
The Six Sigma concept was introduced by Bill Smith in 1986, who was then working at Motorola. Six Sigma was heavily inspired by PDCA and other earlier quality management methodologies. Motorola believes that Six Sigma has saved them $17 billion in lost costs.
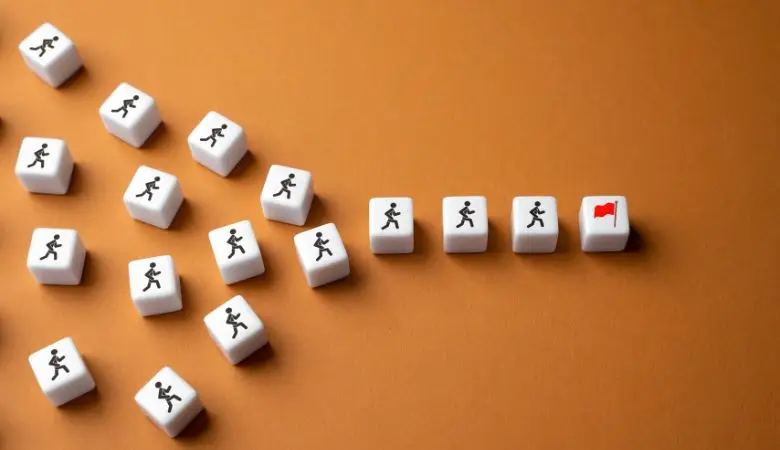
Quality is achieved, according to Six Sigma, when a product or service is produced with an error margin below 3.4 errors per million units produced.
Lean Six Sigma
Combining Lean and Six Sigma has become popular. Both scaling out what does not add value to the customer and larger-scale process improvements have proven effective.
Lean is about working with resources as efficiently as possible and focusing these smaller numbers of resources and work efforts on creating as much value as possible. Lean’s focus on minimizing waste and working better with resource management marries well with Six Sigma’s focus on reducing errors and improving processes and quality by using statistical methods to identify and eliminate causes of variations and defects.
DMAIC: The Model for Improvement
When working with Six Sigma, you will likely work with one of two methods, depending on whether you are aiming for improvement or creating something new. When improvement is the goal, DMAIC methods are often used, which stands for Define, Measure, Analyze, Improve, and Control:
- Define: This is the first step where the project goals, scope, and customer needs are defined. It is important to clearly understand and define the problem to be solved.
- Measure: This is where data is collected to measure current performance. This step is crucial to understanding the baseline and comparing it to performance after improvements.
- Analyze: In this step, data is analyzed to identify the causes of the problems. The goal is to find the root of the problem or the factors that contribute most to it.
- Improve: Based on the analysis in the previous step, solutions are developed to eliminate the causes of the problem. This may involve restructuring processes, implementing new methods, or making changes to existing ways of working.
- Control: The final step is about ensuring that the improvements made are sustainable over time. This may involve implementing control systems, conducting regular follow-ups, and ensuring that the improvements continue to produce the desired results.
By following these steps, organizations can systematically improve processes, increase efficiency, and reduce errors and variations.
DMADV (DFSS): The model for creating something new
The second method is DMADV, also known as DFSS (Design for Six Sigma). It is a methodology within Six Sigma that focuses on creating new processes or products to achieve higher levels of quality. DMADV stands for Define, Measure, Analyze, Design, and Verify.
- Define: This first step defines the project’s goals, scope, and customer needs. It’s important to have a clear understanding of what needs to be accomplished and for whom.
- Measure: This is where you identify and measure the critical quality parameters that are important to the customer. This can include everything from performance criteria to delivery times and cost-effectiveness.
- Analyze: This step analyzes different options to achieve the defined goals. This may include a detailed examination of different design options, processes, or systems.
- Design: Based on the analysis, the new product or process is designed. This often involves an iterative process where different design alternatives are evaluated and refined.
- Verify: The final step is to verify that the new design meets the established quality objectives.
This may involve testing, piloting, and other validation processes to ensure that the product or process performs as intended in the actual use environment.
DMADV is particularly useful when there is no existing process to improve (unlike DMAIC, which focuses on improving pre-existing processes) or when a completely new process or product must be developed to meet new needs or to achieve significantly higher levels of performance.
Tips for ensuring success with Six Sigma
Today, many are faced with intense pressure internally and externally. They are trying to innovate and develop new things faster and better to meet customer needs. The fickle customers and the faster pace place higher demands on quality, flexibility, and efficiency.
What is often forgotten in all new thinking are the old methods and tried and tested tips:
- Make sure stakeholders are on board. Motivate with time savings and improved product or service in the long term and cost savings in the short term. Proper implementation and management commitment are important to achieve the desired results.
- Ensure that knowledge about Six Sigma is constantly disseminated and that sufficient knowledge is available.
- Get to know the customer’s requirements for your product or service.
- Make decisions based on facts (data-driven decision-making).
- Distribute responsibilities among those involved in the project.
- Fight the root cause of the problem, not the symptoms.
- Make quality your number one priority and focus on long-term goals.
- Visualize with (e.g.) flow charts, cause and effect diagrams, and histograms to more easily draw conclusions and create consensus based on needs.
- Use (and strive for) the margin of error allowed.
- Review the work that has been done on repeated occasions to continuously improve (in Six Sigma, and other methodologies, these occasions are called Gate Reviews).
- Management must not show anger when facts (results) are presented to subordinates.
- Data and information that is not disseminated is considered false data.
- The ideal state of quality control is when quality inspection is no longer necessary.
In Six Sigma, it is often thought, and somewhat simplified, that a better product or service makes the customer happier. This is a logical conclusion, but “better” is sometimes difficult to define and people are not always logical. Remember to focus on what the customer wants, use data, continuously improve, be involved, and be thorough.
Six Sigma Belts
Six Sigma uses different belt levels to symbolize knowledge and expertise, similar to those used in martial arts. Each belt represents an increasing level of knowledge, expertise, and responsibility within the Six Sigma methodology. These belts are central to the successful implementation and long-term sustainability of Six Sigma within an organization.
- White Belt: This is the introductory level to Six Sigma. Individuals with a white belt understand the basics of Six Sigma and how it can be applied within an organization.
- Yellow Belt: Individuals have a basic understanding of the Six Sigma process. They may participate in project teams and help identify problems but do not typically lead projects.
- Green Belt: Individuals with a Green Belt have a deeper understanding of Six Sigma and often participate as members or leaders of project teams. They are skilled in using specific tools and techniques for analysis and problem-solving.
- Black Belt: Black Belts are experts in Six Sigma and typically lead large projects. They can apply Six Sigma methods at an advanced level and can also train and coach lower-level people.
- Master Black Belt: This is the highest level in the Six Sigma hierarchy and signals extensive knowledge and experience. These individuals are often responsible for strategically implementing Six Sigma in an organization. They train and coach Black and Green Belts and are typically involved in developing the company’s long-term process improvement strategies.
- Brown Belt: Brown Belt is not traditionally utilized in Six Sigma and is not determined by most organizations.
It is recognized that it takes a long time to get started with and see results from Six Sigma, and therefore it is important to cultivate knowledge about Six Sigma in your organization. Smaller organizations have a harder time achieving success with the method.